Puhutaanpa koksin roolista masuuniprosessissa. Katsotaanpa tarkemmin tämän metallurgisen tuotannon ydintä.
Nykyään rautaa ja terästä valmistetaan masuuniprosessilla, jossa uuni on tärkeä komponentti.
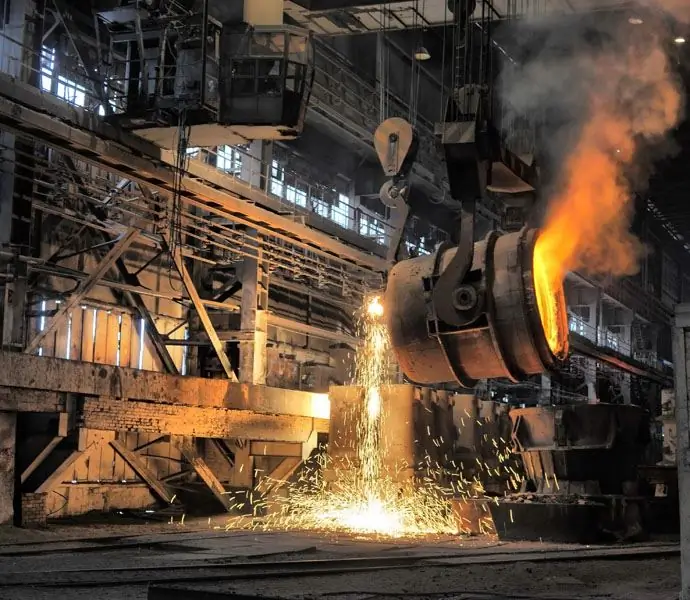
Yksikkötiedot
Harkitse laitteen ominaisuuksia ja tarkoitusta. Masuunin pääprosessit liittyvät koksin sulatukseen. Se on huokoinen materiaali, joka sintrataan hiilimassasta, joka on saatu kalsinoimalla hiiltä ilman ilmakehän happea.
Masuuni on tehokas ja tehokas yksikkö, jossa kuluu huomattava määrä puhallusta ja panosta.
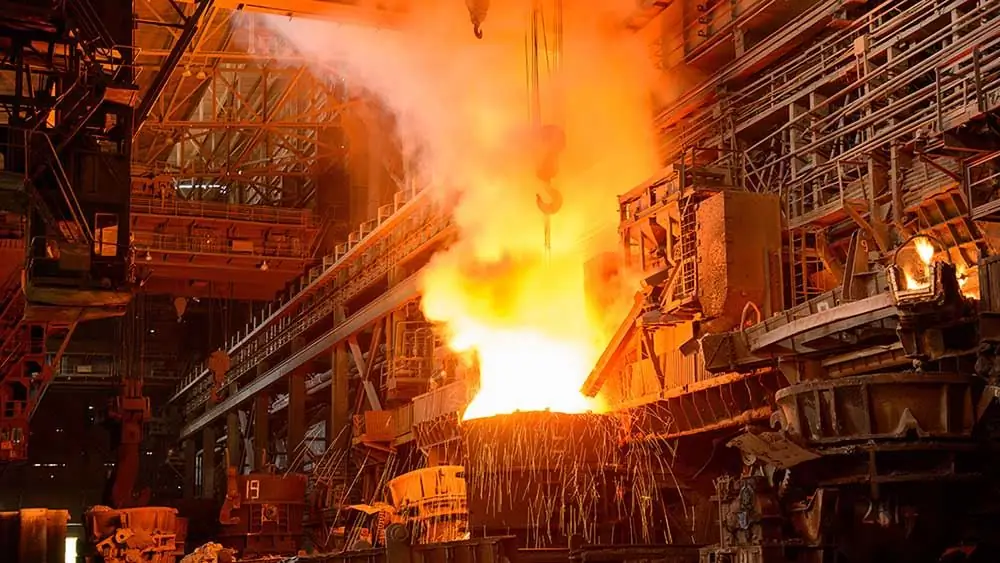
Raaka-aineiden lataus
Nykyaikainen masuuni vaatii materiaalien pysymistä siinä 4-6 tuntia, kaasumaisten aineiden - 3-12 sekuntia. Jos kaasut jakautuvat kokonaan poikkileikkaukselleuuneissa, voit luottaa korkeisiin sulamisnopeuksiin, raudan tuotanto on käynnissä. Masuuniprosessissa otetaan huomioon kaasujen liikkuminen vyöhykkeiden läpi, joilla on pienempi varausvastus. Siksi, kun se ladataan uuniin, suoritetaan säätö, koksin ja sintraus jaetaan uudelleen uunin poikkileikkaukselle siten, että ne eroavat kaasun läpäisevyydestä. Muuten suurempi prosenttiosuus kaasuista poistuu uunista merkittävässä lämpötilassa, mikä vaikuttaa negatiivisesti lämpöenergian käyttöön, masuuniprosessi ei ole täysin tehokas.
Niillä alueilla, joilla on korkea vastus, kaasuseos lämpenee hieman kuumennettuna, lisälämpöä tarvitaan uunin alaosassa, minkä seurauksena raaka-aineiden kulutus kasvaa merkittävästi.
Mitä muita ominaisuuksia on tärkeää ottaa huomioon latauksen aikana? Masuuniprosessi harkkoraudan valmistukseen on energiaintensiivistä tuotantoa. Tästä syystä uunin seinien lähellä käytetään kerrosta vähemmän kaasua läpäisevää agglomeraattia, ja keskellä kasvatetaan koksikerrosta, minkä ansiosta kaasuvirtaus jakautuu uudelleen keskelle. Materiaalit ovat tasaisin välein kehän ympärillä.
Lataus ladataan erillisinä osina - syötteinä. Yksi annos koostuu useista skipsistä, malmiosasta (agglomeraatista), koksista. Asiantuntijat määrittävät alkuperäisten ainesosien suhteen.
Masuuniprosessi mahdollistaa raaka-aineiden yhteissyötön, jossa koksi ja sintrausjätteet kerätään suurelle kartiolle ja ladataan sitten uuniin.
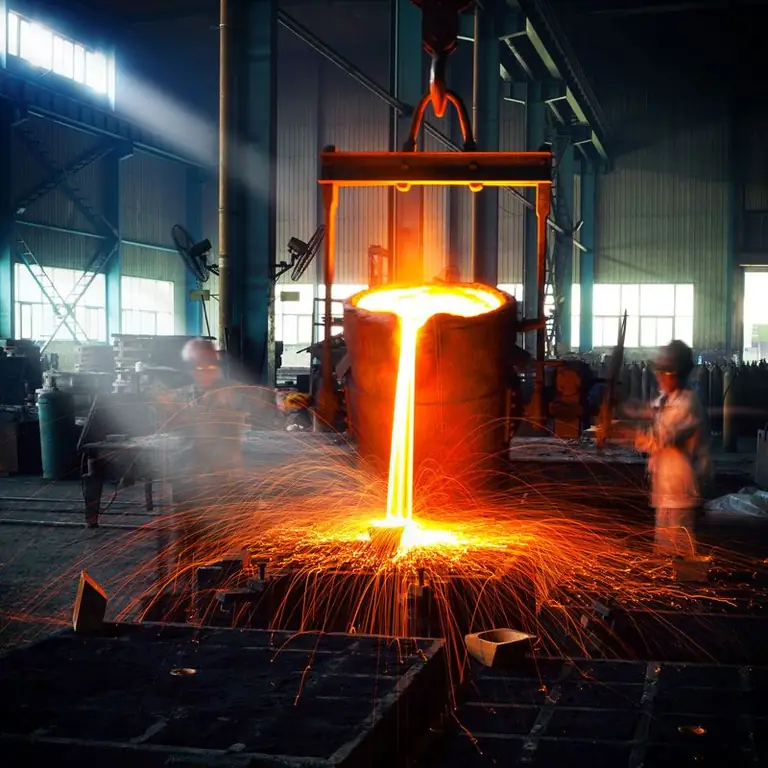
Erän jakelun säätö
Koksin ja agglomeraatin jakautumista latvojen poikkileikkaukselle ohjataan seuraavilla menetelmillä:
- raaka-aineiden järjestyksen muuttaminen isolla kartiolla;
- jaettu ja jaettu tarjoilu koskee;
- liikkuvat levyt asennetaan lähelle yläosan seiniä.
Masuuniprosessiin kuuluu tiettyjen bulkkimateriaalien käyttöönoton säännönmukaisuuksien huomioon ottaminen:
- raaka-aineiden asettaminen suuresta kartiosta putoavien kohokuvioiden päälle - kampa;
- Patauksen harjalle (putoamiskohdassa) hienojakoisia hiukkasia kerääntyy, suuret palat vierivät alas harjanteen juurelle, joten tällä alueella panoksen kaasunläpäisevyys on suurempi;
- harjaan vaikuttaa täyttöaste yläosassa sekä etäisyys suurella kartiolla;
- suuri kartio ei laskeudu kokonaan alas, joten pienet koksinpalat pääsevät reunalle.
Pääosin uunin keskikohta vastaanottaa materiaalia syöttösäiliöistä, jotka ladattiin viimeisenä suureen kartioon. Jos muutat latausjärjestystä, voit saada materiaalit jakautumaan uudelleen yläosan poikkileikkauksen poikki.
Käytetyn panoksen jakautumisen ohjaamiseksi uunin tilavuuteen käytetään kahta kartiolaitetta. Viime aikoina jotkut masuunit on varustettu siirrettävillä levyillä lähellä yläosan seiniä, jolloin voit muuttaa k altevuuskulmaa ja siirtää niitä vaakatasossa.
Latjoille putoavat latauksen palaset heijastuvat niistä, jolloin voit ohjata raaka-aineen tietyille kannen vyöhykkeille.
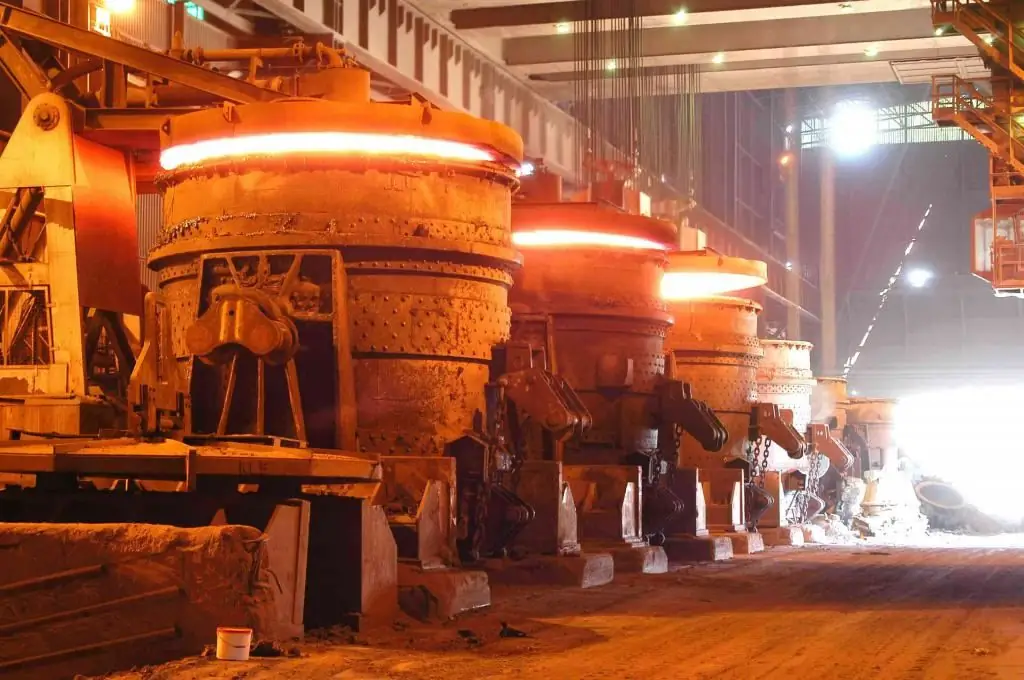
Liedetei kartiota
Uuneissa, joissa ei ole kartiolatauslaitetta, raaka-aineiden lastaus tapahtuu kahden vuorotellen avautuvan sulkusuppilon kautta. Raaka-aineet toimitetaan niille k altevilla hihnakuljettimilla, joille koksi ja sintraus sijaitsevat selkein välein. Yksi annos tulee hihn alta yhteen bunkkeriin, jonka jälkeen se puretaan uunin yläosaan pyörivää k altevaa alustaa pitkin. Purkujakson aikana ne tekevät noin kymmenen täyttä kierrosta kiinteän keskiakselin ympäri.
Latausjakso
Sitä on tapana kutsua toistuvaksi määräksi latausmateriaaleja. Suurin annos määräytyy latausmekanismin lukkosuppilon tilavuuden mukaan. Annosten lukumäärä yhdessä syklissä voi olla 5 - 14. Kuinka saada masuuniprosessin tuotteet täyteen? Jotta voisimme vastata tähän kysymykseen, katsotaanpa tarkemmin prosessin ydintä. Kun seoksen hiilidioksidipitoisuus on lisääntynyt, matala lämpötila edistää lämmönvaihdon ja kemiallisten prosessien täydellisyyttä masuunissa. Jotta laite toimisi taloudellisesti ja intensiivisesti, hiilidioksidin määrällistä pitoisuutta uunin akselilla ja kehällä tulisi vähentää ja yhden tai kahden metrin korkeudella seinistä - lisätä.
Lämpötilan säätö uusissa uuneissa toteutetaan viemällä anturit kotelossa olevien reikien läpi. Pakollinen kaikissa prosesseissa on täyttötason ohjaus yläreunassa.
Innovaatioiden joukossa on kosketuksettomien tasonmittausmenetelmien käyttö, jotka perustuvat mikroa alto- ja infrapuna-anturien lukemiin.
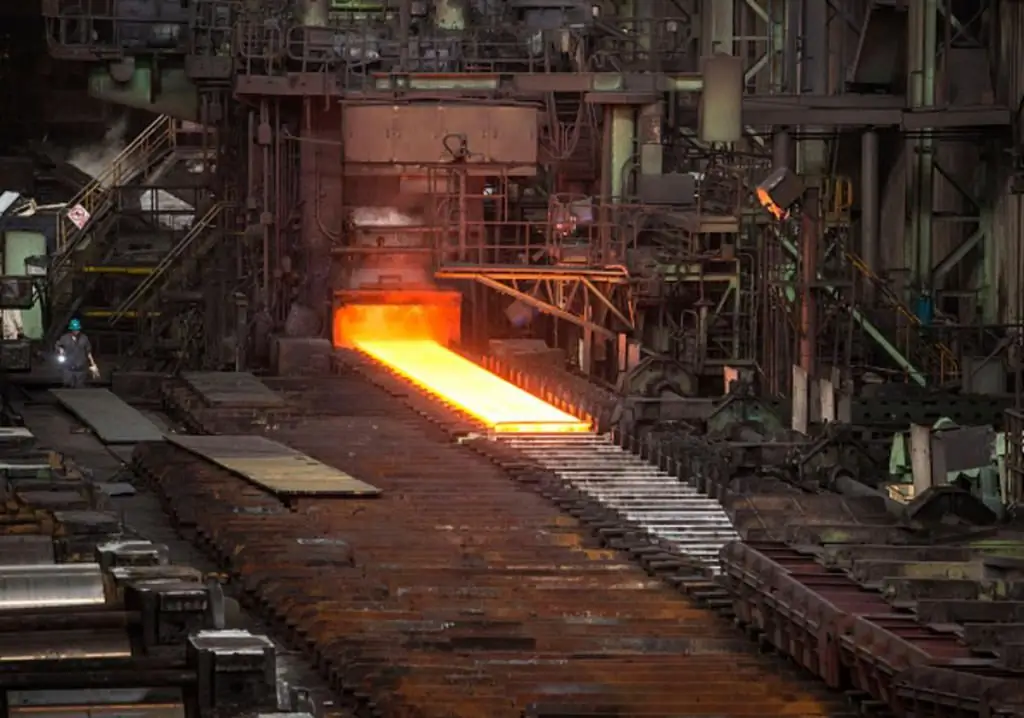
Lämpötilan jakeluominaisuudet
Kuumennetulla puhalluksella syötettävän lämmön lisäksi kaasujen ja panoksen lämmittämisen päälämmönlähteenä, t alteenotossa ja lämpöhäviöiden kompensoinnissa, häviöitä voidaan kompensoida vapautuvalla lämmöllä polttoaineen palamisen aikana tulisijan yläosassa. Kun kaasumaiset tuotteet liikkuvat tulisijasta ylöspäin, lämpö laskeutuu panoskylmiin materiaaleihin ja tapahtuu lämmönvaihtoa. Samanlainen prosessi selittää lämpötilan putoamisen 1400 astetta 200 asteeseen uunin yläosan ulostulossa.
Poista ylimääräinen kosteus
Katsotaanpa tärkeimpiä fysikaalisia ja kemiallisia prosesseja masuunissa. Masuuniin ladattavassa panoksessa on hygroskooppista kosteutta. Esimerkiksi koksin koostumuksessa sen pitoisuus voi olla jopa viisi prosenttia. Kosteus haihtuu nopeasti pinn alta, joten sen poistamiseen tarvitaan lisälämpöä.
Hydraatin kosteutta ilmaantuu, kun ruskeaa rautamalmia ja kaoliinia ladataan masuuniin. Nykyaikaisen raudan tuotannon ongelman ratkaisemiseksi näitä malmeja ei käytännössä käytetä raaka-aineina.
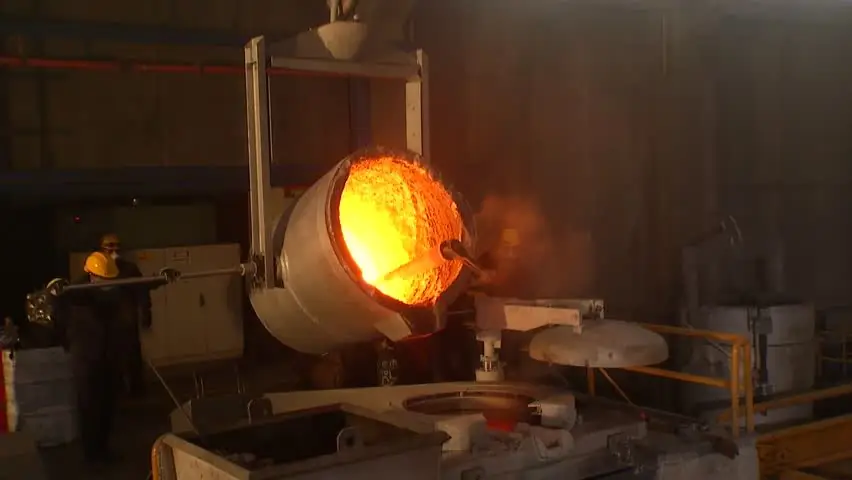
Karbonaattien hajoamisprosessit
Hiilihapon suolat voivat päästä masuuniin. Kuumentaessaan ne hajoavat kalsiumin ja hiilen oksideiksi, ja prosessiin liittyy riittävä määrä energiaa.
Viime aikoina masuuniin ei ole ladattu juuri lainkaan malmia. Mikä on sulatteiden rooli masuuniprosessissa? Ne lisäävät sen tehokkuuttamahdollistaa tuotantokustannusten alentamisen. Fluxed sintterin käytön ansiosta kalkkikiven täydellinen poistaminen masuunin panoksesta voi saavuttaa merkittäviä koksin säästöjä. Kalkkikiven hajoamisprosessi agglomeroitumisen aikana saadaan aikaan huonolaatuisen polttoaineen palamisella.
raudan t alteenotto
Rautaa syötetään masuuniin oksidien muodossa. Prosessin päätavoitteena on maksimoida raudan uuttaminen oksideista pelkistämällä. Prosessin ydin on poistaa happi, hiiltä, hiilimonoksidia ja vetyä käytetään tähän. Pelkistystä hiilellä kutsutaan suoraksi prosessiksi ja reaktiota kaasumaisten aineiden kanssa epäsuoraksi vuorovaikutukseksi. Mitkä ovat niiden tunnusmerkit? Suorassa reaktiossa hiiltä kuluu, minkä seurauksena sen määrä vähenee merkittävästi. Toisen tyyppinen raudan pelkistys oksideista vaatii ylimäärän vetyä.
Prosessi tuottaa kiinteää rautaa. Valuraudan t alteenottoaste on 99,8 %. Siten vain 0,2 -1 % muuttuu kuonaksi.
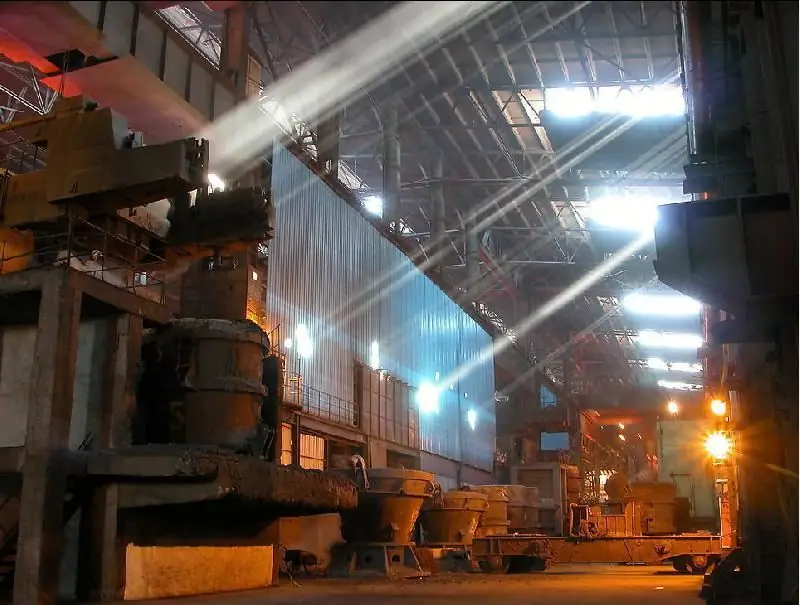
Mangaanivaluraudan sulatus
Uudelleenvalmistetun valuraudan sulatuksessa mangaani tulee masuuniin agglomeraatin muodossa. Joissakin määrin mangaanimalmit mangaanisilikaattien muodossa edistävät mangaanivaluraudan tuotantoa.
Mangaanioksideista t alteenotto tapahtuu vaiheittain. Prosessin loppuun saattamiseksi uuniin on asetettava korkeat lämpötilat. Harkkoraudan sulatusprosessiin liittyymangaanin vähentäminen vain suhteessa 55-65%. Tällä hetkellä mangaanimalmien ja mangaanin niukkuuden vuoksi teknologiaketjussa on käytetty pieni määrä mangaanivalurautaa. Vaihtaessa vähämangaanipitoisiin valuraudoihin on mahdollista säästää paitsi itse mangaania myös koksia, koska sen kulutus metallin suoraan pelkistykseen vähenee.
Johtopäätös
Masuuniprosessi on yksi tärkeimmistä raudan ja teräksen sulatuksen menetelmistä. Riippuen siitä, mitä komponentteja lisätään alkuperäiseen seokseen, tällä hetkellä saadaan erilaisia valmiita tuotteita. Tuloksena olevan valuraudan ja teräksen käyttöalueista erotamme: koneenrakennus, kemianteollisuus, lääketiede, instrumenttien valmistus.